Laboratory ball mills, despite their smaller scale compared to industrial counterparts, embody the same fundamental principles of size reduction through impact and attrition. However, the unique demands of research and development necessitate specific design considerations. This chapter delves into the critical aspects of laboratory ball mill design, emphasizing the need for precision, versatility, and efficiency in a compact footprint.
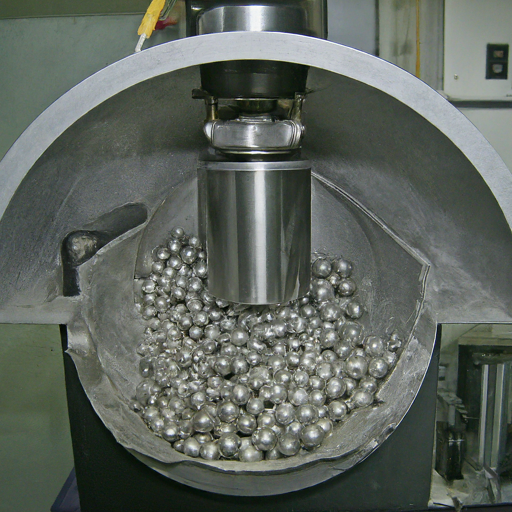
Basic Principles of Operation
At the core of laboratory ball mill operation lies the principle of kinetic energy transfer. As the mill rotates, the grinding media (typically steel or ceramic balls) are lifted by centrifugal force and subsequently cascade down, impacting the material to be ground. This impact, coupled with the frictional forces between the media and the material, results in size reduction.
Critical Speed
A critical design parameter is the critical speed, the rotational speed at which the grinding media just begin to form a continuous annular layer on the mill’s inner wall. Operating above this speed leads to centrifuging action, while below it, a cascading action prevails. Laboratory ball mills often operate in the cascading regime to maximize grinding efficiency and prevent excessive wear on the mill components.
Power Requirements
The power input to a laboratory ball mill is significantly lower than its industrial counterpart due to the smaller scale. However, efficient power utilization is crucial for minimizing energy consumption and maximizing productivity. Factors influencing power requirements include the type of material being ground, the desired particle size, and the fill level of the grinding media.
Design Considerations
Mill Geometry
Laboratory ball mills typically exhibit a cylindrical or jar-shaped geometry. The choice of geometry influences the grinding efficiency and the distribution of grinding media. Cylindrical mills tend to provide a more uniform grinding action, while jar-mills can be more effective for certain types of materials.
Mill Material
The material of the mill body and liner is critical. Stainless steel is commonly used for its corrosion resistance and strength. However, for abrasive materials or specific applications, ceramic or hardened steel liners may be necessary.
Grinding Media
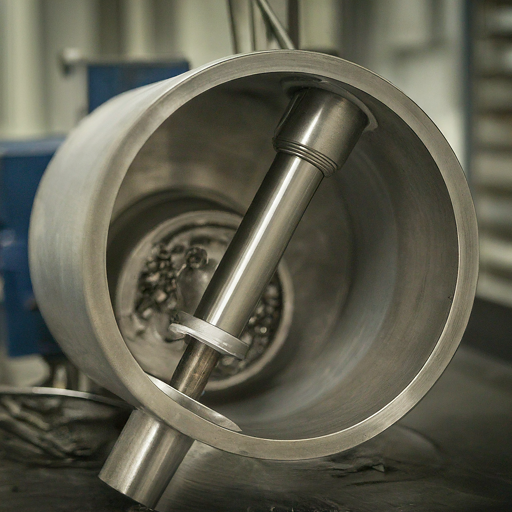
The selection of grinding media is crucial. Steel balls are the most common choice, but ceramic, agate, or tungsten carbide balls may be required for specific applications. The size and density of the grinding media influence the grinding efficiency and the energy required for size reduction.
Mill Drive System
Laboratory ball mills typically employ electric motors to drive the grinding chamber. The motor’s power, speed control, and torque characteristics are essential for precise control of the grinding process.
Sealing and Containment
Effective sealing is vital to prevent material loss and contamination. Laboratory ball mills often incorporate rubber or PTFE gaskets to ensure airtightness. For hazardous or toxic materials, additional containment measures may be necessary.
Performance Evaluation
The performance of a laboratory ball mill is assessed based on factors such as particle size distribution, grinding efficiency, power consumption, and material recovery. Particle size analysis techniques, such as laser diffraction or sieve analysis, are employed to characterize the ground product.
Grinding Kinetics
Understanding the grinding kinetics is essential for optimizing the milling process. Parameters such as grinding time, media-to-material ratio, and mill speed influence the rate of particle size reduction. Kinetic models can be developed to predict the grinding behavior of different materials.
Scale-Up Considerations
While laboratory ball mills are primarily used for research and development, understanding scale-up principles is important for translating results to industrial production. Geometric similarity, power scaling, and material properties are key factors to consider when scaling up the process.
Special Considerations for Laboratory Applications
Sample Size: Laboratory ball mills typically handle small sample quantities, necessitating careful attention to sample loading and discharge.
Material Handling: The ability to handle a wide range of materials, including dry, wet, and hazardous substances, is often required.
Versatility: Laboratory ball mills should be adaptable to various grinding conditions and applications.
Cleaning and Maintenance: Ease of cleaning and maintenance is essential for preventing cross-contamination and ensuring reliable operation.
Laboratory ball mill design is a multifaceted discipline that requires a balance of theoretical understanding and practical considerations. By carefully considering the factors discussed in this chapter, engineers can develop ball mills that meet the specific needs of research and development applications.
Would you like to delve deeper into a specific aspect of laboratory ball mill design, such as grinding media selection, scale-up challenges, or the design of specialized mills for specific materials?