Die Laborkugelmühle,
ein Eckpfeiler der Materialwissenschaft, erfordert eine sorgfältige Konstruktion und einen sorgfältigen Betrieb, um konsistente und zuverlässige Ergebnisse zu erzielen. Dieser Artikel befasst sich mit zehn kritischen Faktoren, die, wenn sie beachtet werden, die Leistung und Langlebigkeit von Laborkugelmühlen erheblich verbessern können.
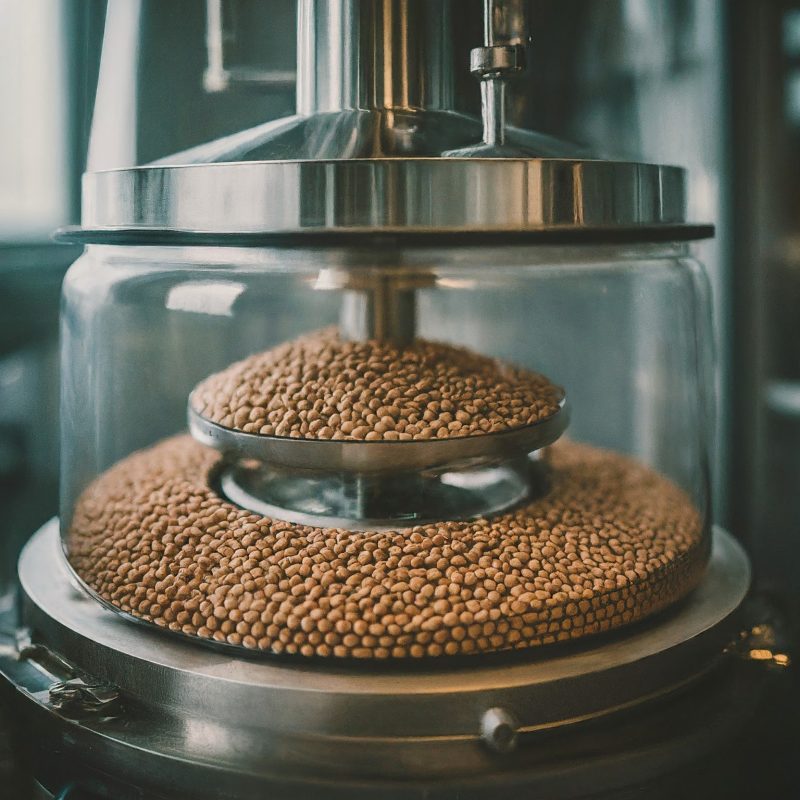
- Materielle Kompatibilität: Das Fundament des Erfolgs
Die Auswahl der Materialien für die Mühlenkomponenten und die Mahlkörper ist von größter Bedeutung. Die Kompatibilität zwischen den Materialien ist entscheidend, um Verunreinigungen, Verschleiß und Ausfälle zu vermeiden. Faktoren wie Korrosionsbeständigkeit, Härte und thermische Eigenschaften müssen genauestens berücksichtigt werden. So wird beispielsweise Edelstahl aufgrund seiner Korrosionsbeständigkeit häufig bevorzugt, während Keramik oder Wolframkarbid für abrasive Materialien erforderlich sein können.
- Auswahl von Mahlkörpern: Eine Symphonie aus Größe und Material
Die Mahlkörper, in der Regel Kugeln aus Stahl, Keramik oder Achat, spielen eine zentrale Rolle im Mahlprozess. Größe, Menge und Material der Mahlkörper haben einen erheblichen Einfluss auf die Mahlleistung und die endgültige Partikelgröße. Eine sorgfältige Auswahl auf der Grundlage des zu verarbeitenden Materials und des gewünschten Ergebnisses ist unerlässlich.
- Kammer-Design: Das Gefäß der Transformation
Die Konstruktion der Mühlenkammer ist entscheidend für die Optimierung des Mahlprozesses. Faktoren wie Kammervolumen, Form und Material beeinflussen die Mahlleistung und den Energieverbrauch. Eine gut gestaltete Kammer fördert einen effizienten Materialfluss, verhindert tote Zonen und minimiert den Verschleiß.
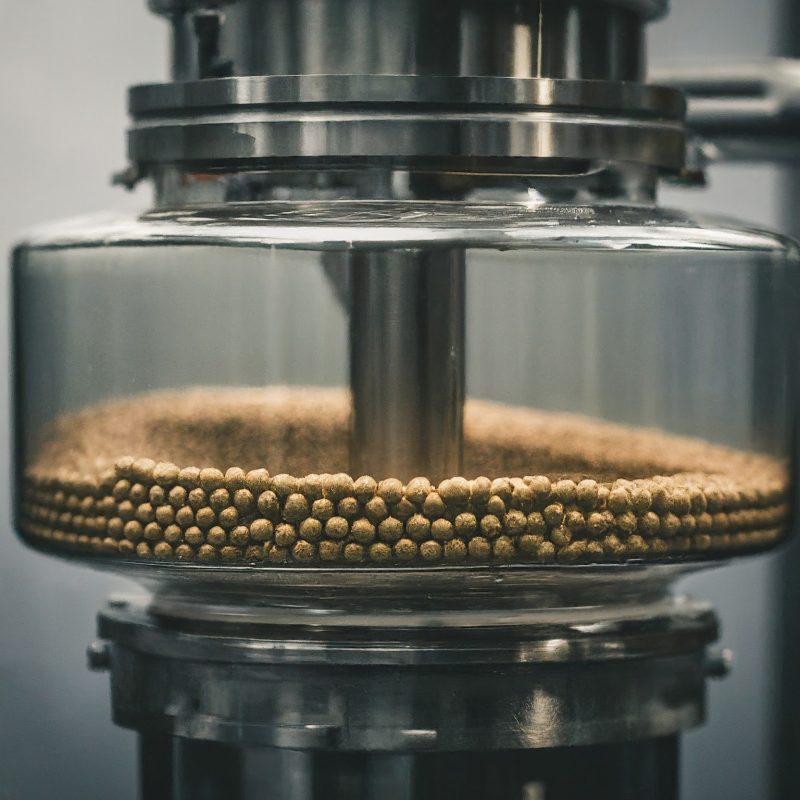
- Geschwindigkeit und Leistung: Die treibende Kraft
Die Rotationsgeschwindigkeit der Mühle ist ein kritischer Parameter. Eine zu hohe Drehzahl kann zu Überhitzung und geringerer Mahlleistung führen, während eine zu niedrige Drehzahl eine unzureichende Zerkleinerung der Partikel zur Folge haben kann. Die dem Motor zugeführte Leistung muss ausreichend sein, um die Mahlkörper anzutreiben und den Widerstand des zu verarbeitenden Materials zu überwinden.
- Kühlung und Belüftung: Aufrechterhaltung optimaler Bedingungen
Die Wärmeentwicklung ist ein fester Bestandteil des Schleifprozesses. Eine wirksame Kühlung ist von entscheidender Bedeutung, um eine Verschlechterung des Materials zu verhindern und die Effizienz des Schleifens zu optimieren. Angemessene Belüftung ist auch wichtig, um Staub zu entfernen und eine sichere Arbeitsumgebung zu erhalten.
- Materialbelastung: Die Kunst des Gleichgewichts
Die Menge des in die Mühle eingebrachten Materials hat einen erheblichen Einfluss auf den Mahlprozess. Eine Überladung kann zu ineffizientem Mahlen und übermäßigem Verschleiß führen, während eine Unterladung die Produktivität verringern kann. Die Optimierung der Materialbeladung ist für das Erreichen gleichmäßiger Ergebnisse von entscheidender Bedeutung.
- Optimierung der Schleifzeit: Die Zeit ist das Wesentliche
Die Bestimmung der optimalen Mahldauer erfordert eine sorgfältige Berücksichtigung der Materialeigenschaften und der gewünschten Partikelgrößenverteilung. Eine zu lange Mahldauer kann zu Übermahlung und Verunreinigung führen, während eine zu kurze Mahldauer zu einer suboptimalen Partikelgrößenreduzierung führen kann.
- Analyse der Partikelgröße: Überwachung der Fortschritte
Die regelmäßige Überwachung der Partikelgrößenverteilung ist für die Prozesskontrolle und -optimierung unerlässlich. Verfahren zur Analyse der Partikelgröße, wie z. B. Laserbeugung oder Siebanalyse, können wertvolle Einblicke in den Mahlprozess geben und dabei helfen, verbesserungswürdige Bereiche zu identifizieren.
- Wartung und Reinigung: Der Schlüssel zur Langlebigkeit
Regelmäßige Wartung und Reinigung sind entscheidend für die Erhaltung der Leistungsfähigkeit der Mühle und die Verlängerung ihrer Lebensdauer. Die Entfernung von angesammeltem Material, die Inspektion der Verschleißteile und die Schmierung der beweglichen Teile sollten gemäß den Empfehlungen des Herstellers durchgeführt werden.
- Bedienerschulung und Sicherheit: Der menschliche Faktor
Eine ordnungsgemäße Schulung des Bedieners ist für den sicheren und effizienten Betrieb der Laborkugelmühle unerlässlich. Um Unfälle zu vermeiden und eine optimale Leistung zu gewährleisten, ist es wichtig, die Fähigkeiten, Grenzen und Sicherheitsverfahren der Maschine zu kennen.
Durch sorgfältige Beachtung dieser zehn Faktoren können Forscher und Ingenieure die Leistung und Zuverlässigkeit ihrer Laborkugelmühlen erheblich verbessern, was zu besseren Versuchsergebnissen und einer höheren Gesamteffizienz führt.
Hinweis: Dieser Artikel gibt einen allgemeinen Überblick über mögliche Fallstricke und Strategien für den Betrieb von Laborkugelmühlen. Spezifische Anwendungen und Materialeigenschaften können zusätzliche Überlegungen und Optimierungen erfordern.