Within the realm of mechanical design,achieving precise control over particle size plays a pivotal role in diverse fields. The attrition stirred ball mill, also known as an attritor mill, emerges as a powerful tool for this endeavor. Drawing inspiration from the meticulous approach of Mechanical Design, this article delves into the inner workings of stirred ball mills, exploring their design principles, operating mechanisms, and the interplay between agitation and size reduction.

- The Grinding Landscape: A Spectrum of Approaches
The quest for fine powders necessitates a diverse arsenal of size reduction techniques. Among these techniques, ball milling stands out for its versatility and effectiveness. Traditional ball mills rely on the tumbling action of a rotating drum or the centrifugal forces within a horizontal mill to achieve size reduction. Attrition stirred ball mills, however, employ a fundamentally different approach – agitation and attrition.
- The Core Design: Unveiling the Agitation Mechanism
The heart of an attrition stirred ball mill lies in its agitation system. Unlike traditional ball mills, the grinding chamber in an attritor mill remains stationary. Instead, a high-speed rotating shaft equipped with agitator elements is situated within the chamber. These agitator elements, often impellers or discs, churn the grinding media and material mixture, creating a turbulent and highly agitated environment.
Impeller Design: Impellers are typically multi-bladed propellers that generate a powerful axial flow within the chamber. The design of the impeller blades (shape, pitch, and number) influences the flow characteristics and the interaction with the grinding media and material.
Disc Agitators: These agitators are disc-shaped elements that rotate about a central shaft. They can be configured in various ways, with single or multiple discs, to generate a radial flow pattern within the chamber.
- The Symphony of Size Reduction: Unveiling the Grinding Action
The size reduction process in an attrition stirred ball mill unfolds through a carefully orchestrated interplay between agitation, media selection, and particle interactions:
Intense Agitation: The high-speed rotation of the agitator elements creates a turbulent flow within the chamber. This flow propels the grinding media and the material to be ground in a complex, three-dimensional motion.
Media Selection: Similar to traditional ball mills, attrition stirred ball mills utilize grinding media, typically hardened steel or ceramic balls. The size and density of the grinding media influence the impact forces and the overall grinding efficiency.
Attrition Grinding: As the grinding media are propelled by the agitated flow, they collide not only with each other but also with the particles of the material. This collisional interaction breaks down the larger particles into progressively finer sizes. The attrition mechanism differentiates stirred ball mills from impact grinding mills where the focus is on direct collisions between the grinding media and the material.
Shear Forces: The turbulent flow generated by the agitator can also create shear forces within the mixture. These shear forces further contribute to the size reduction process, particularly for softer materials.
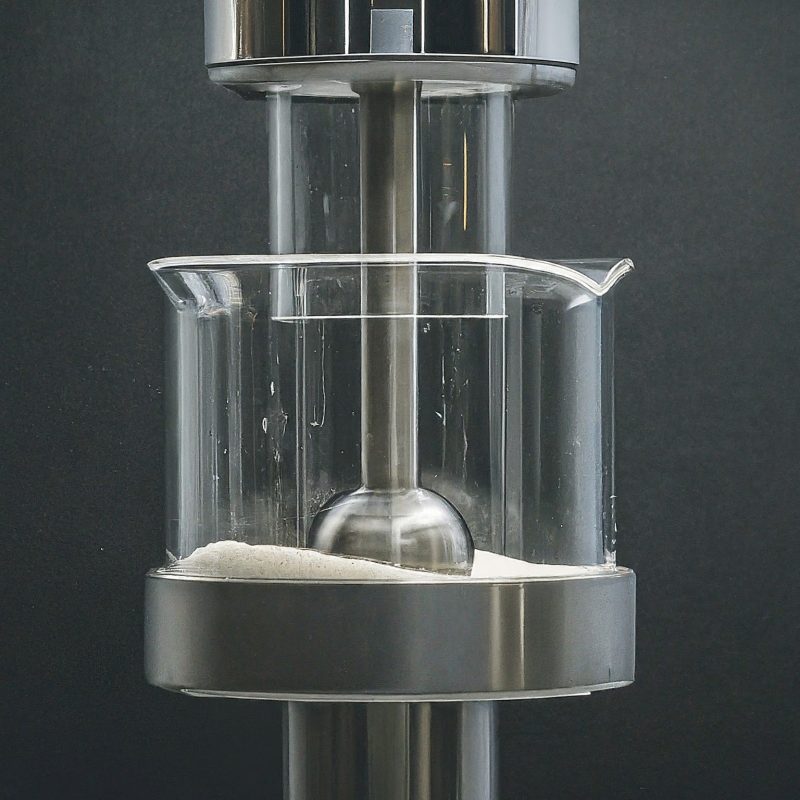
- Unveiling the Grinding Chamber: Design Considerations
The design of the grinding chamber in an attrition stirred ball mill plays a crucial role in optimizing performance and achieving desired particle size distributions. Here, we explore some key aspects:
Chamber Shape: Cylindrical chambers are most common. However, tapered designs might be incorporated to improve solids suspension and prevent settling of the grinding media at the bottom of the chamber.
Liner Material: The chamber walls are often lined with wear-resistant materials like high-chrome cast iron or ceramic tiles to withstand the abrasive action of the grinding media and the material.
Feed and Discharge Systems: Attrition stirred ball mills can operate in both batch and continuous modes. The design of the feed and discharge systems must be carefully considered to ensure efficient material flow and prevent particle size classification within the mill.
- A Spectrum of Applications: Beyond the Basics
The versatility of attrition stirred ball mills extends to a wide range of applications across various disciplines:
Chemical Processing: These mills are employed for size reduction of pigments, catalysts, and other chemical intermediates, enabling precise control over particle size distribution for optimized reaction rates and product quality.
Pharmaceutical Manufacturing: Attrition stirred ball mills are utilized for micronization of active pharmaceutical ingredients (APIs). This enhances drug delivery and bioavailability of medications.
Food Science: Precise size reduction of food ingredients like spices, cocoa powder, and sweeteners allows for the creation of desired textures and functionalities in food products.
Environmental Remediation: Attrition stirred ball mills can be used for the processing of contaminated soils or sediments, facilitating the removal of pollutants through size reduction and subsequent separation techniques.