The laboratory jar mill, a versatile tool in the realm of materials science, provides precise control over particle size reduction. To maximize its potential, understanding its operation and optimization techniques is crucial. This article delves into the intricacies of lab jar mill usage, drawing inspiration from the meticulous approach of Mechanical Design.
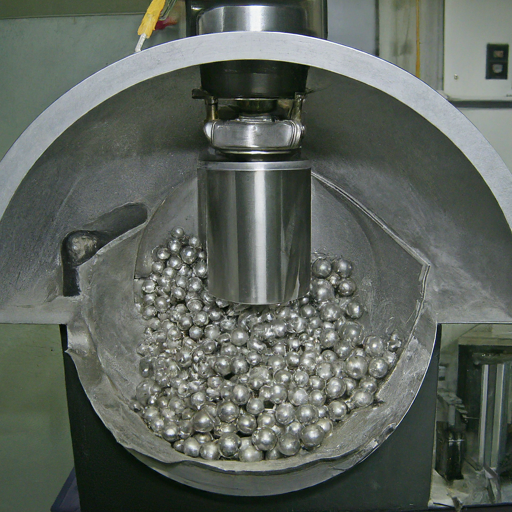
- Understanding the Lab Jar Mill
A lab jar mill comprises a cylindrical chamber containing grinding media, typically ceramic or steel balls. The chamber rotates at a controlled speed, causing the grinding media to cascade and impact the material, resulting in size reduction. Key components include:
Chamber: Houses the grinding media and material.
Drive System: Powers the rotation of the chamber.
Grinding Media: The balls that impact and grind the material.
Lid and Seals: Ensure containment and prevent contamination.
- Preparing for Operation
Before commencing any operation, it’s crucial to:
Select Appropriate Grinding Media: The type and size of grinding media influence particle size distribution. Ceramic balls are ideal for contamination-sensitive materials, while steel balls offer a balance of cost and performance.
Load Material: The amount of material loaded should be within the recommended range to prevent overloading and ensure optimal grinding efficiency.
Secure the Lid: Ensure the lid is securely fastened to prevent accidents and material loss.
Check for Balance: An unbalanced load can cause excessive vibration and damage the mill.
- The Grinding Process
The grinding process involves the following steps:
Start-up: Initiate the mill at a low speed to allow the grinding media to distribute evenly.
Acceleration: Gradually increase the speed to the desired operating speed.
Grinding: Maintain the set speed for the required grinding time.
Cool-down: Allow the mill to cool down before opening the lid.
Material Discharge: Carefully remove the ground material.
- Key Parameters Influencing Grinding Performance
Several factors influence the grinding process:
Grinding Media: The type, size, and quantity of grinding media significantly impact particle size distribution.
Rotation Speed: Higher speeds generally lead to finer particles but can also generate heat and reduce grinding media life.
Grinding Time: The duration of the grinding process affects particle size reduction.
Material Load: The amount of material loaded influences grinding efficiency and prevents overloading.
Temperature Control: For temperature-sensitive materials, cooling systems might be necessary.
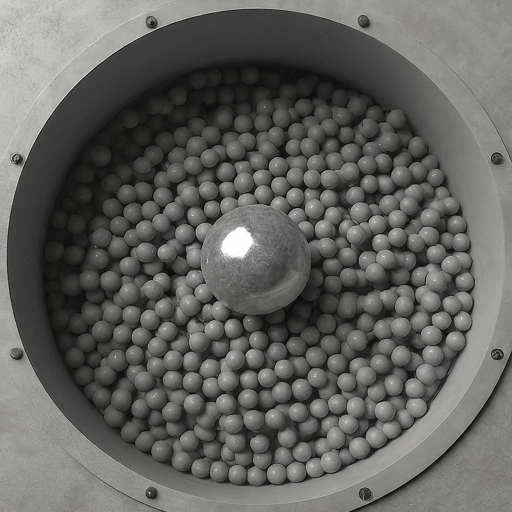
- Troubleshooting Common Issues
Common issues include:
Overheating: Reduce the grinding time or load, or implement cooling measures.
Inconsistent Grinding: Check for uneven grinding media distribution or material overloading.
Contamination: Ensure proper cleaning and sealing of the mill.
Equipment Failure: Regular maintenance and inspection are crucial.
- Safety Considerations Wear protective gear, including safety glasses and gloves.
Avoid touching the mill while it’s operating.
Securely fasten the lid before starting the mill.
Follow manufacturer’s safety guidelines. - Optimization and Experimentation
Achieving optimal grinding results often requires experimentation. By systematically varying parameters like grinding media, speed, and time, it’s possible to fine-tune the process for specific materials.
By understanding the fundamental principles of lab jar mill operation and diligently addressing potential issues, researchers and engineers can maximize the efficiency and effectiveness of this valuable tool.