The laboratory ball mill,
a cornerstone of material science, demands meticulous design and operation to yield consistent and reliable results. This article delves into ten critical factors that, when addressed, can significantly enhance the performance and longevity of laboratory ball mills.
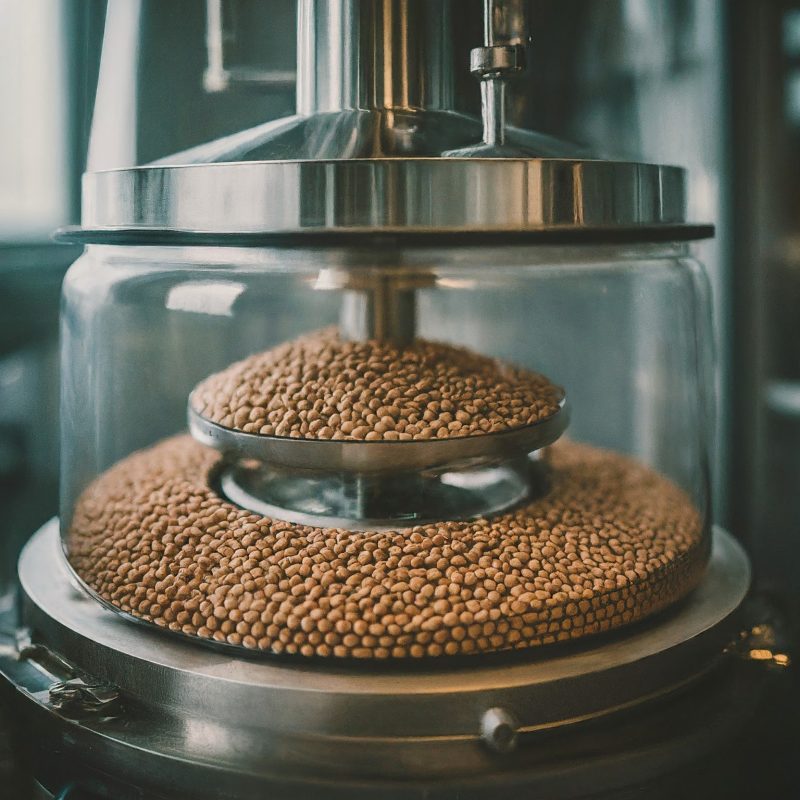
- Material Compatibility: The Foundation of Success
The choice of materials for both the mill’s components and the grinding media is paramount. Compatibility between the materials is crucial to prevent contamination, wear, and equipment failure. Factors such as corrosion resistance, hardness, and thermal properties must be meticulously considered. For instance, stainless steel is often a preferred choice for its corrosion resistance, while ceramic or tungsten carbide may be necessary for abrasive materials.
- Grinding Media Selection: A Symphony of Size and Material
The grinding media, typically balls made of steel, ceramic, or agate, play a pivotal role in the milling process. The size, quantity, and material of the grinding media significantly influence the grinding efficiency and final particle size. A careful selection based on the material being processed and the desired output is essential.
- Chamber Design: The Vessel of Transformation
The design of the mill’s chamber is critical for optimizing the grinding process. Factors such as chamber volume, shape, and material influence the grinding efficiency and energy consumption. A well-designed chamber promotes efficient material flow, prevents dead zones, and minimizes wear and tear.
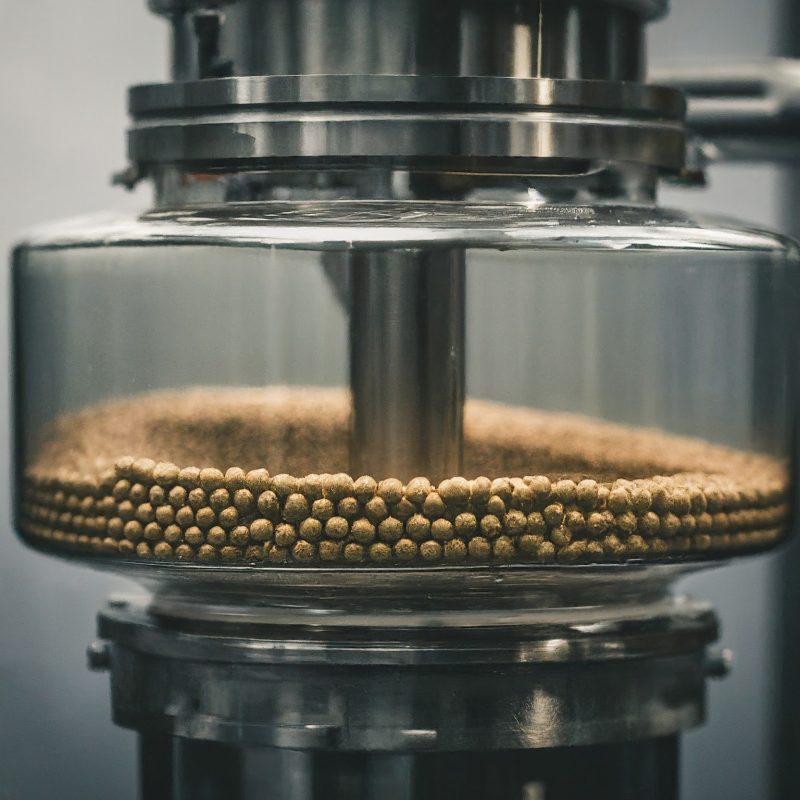
- Speed and Power: The Driving Force
The rotational speed of the mill is a critical parameter. Excessive speed can lead to overheating and reduced grinding efficiency, while insufficient speed can result in inadequate particle size reduction. The power supplied to the motor must be sufficient to drive the grinding media and overcome the resistance of the material being processed.
- Cooling and Ventilation: Maintaining Optimal Conditions
Heat generation is an inherent aspect of the grinding process. Effective cooling is crucial to prevent material degradation and optimize grinding efficiency. Adequate ventilation is also essential to remove dust and maintain a safe working environment.
- Material Loading: The Art of Balance
The amount of material loaded into the mill significantly impacts the grinding process. Overloading can lead to inefficient grinding and excessive wear, while underloading can reduce productivity. Optimizing the material load is essential for achieving consistent results.
- Grinding Time Optimization: Time is of the Essence
Determining the optimal grinding time requires careful consideration of material properties and desired particle size distribution. Excessive grinding can lead to over-grinding and contamination, while insufficient grinding time may result in suboptimal particle size reduction.
- Particle Size Analysis: Monitoring Progress
Regular monitoring of the particle size distribution is essential for process control and optimization. Particle size analysis techniques such as laser diffraction or sieve analysis can provide valuable insights into the grinding process and help identify areas for improvement.
- Maintenance and Cleaning: The Key to Longevity
Regular maintenance and cleaning are crucial for preserving the mill’s performance and extending its lifespan. Removal of accumulated material, inspection of wear components, and lubrication of moving parts should be performed according to the manufacturer’s recommendations.
- Operator Training and Safety: The Human Factor
Proper operator training is essential for safe and efficient operation of the laboratory ball mill. Understanding the machine’s capabilities, limitations, and safety procedures is crucial to prevent accidents and ensure optimal performance.
By diligently addressing these ten factors, researchers and engineers can significantly enhance the performance and reliability of their laboratory ball mills, leading to improved experimental outcomes and overall efficiency.
Note: This article provides a general overview of potential pitfalls and strategies for laboratory ball mill operation. Specific applications and material properties may require additional considerations and optimizations.