Grinding Machine for Grinding Ceramic Glaze Slurry
소개
Ceramic glaze slurry, a critical component in ceramic production, requires precise particle size reduction for optimal application and performance. Grinding machines play a vital role in achieving the desired consistency and properties of ceramic glaze slurry. This article explores the types of grinding machines suitable for this application, factors to consider when selecting the right equipment, and key considerations for achieving optimal results.
Types of Grinding Machines for Ceramic Glaze Slurry
Several types of grinding machines are commonly used for processing ceramic glaze slurry, each with its specific characteristics and applications.
Ball Mills
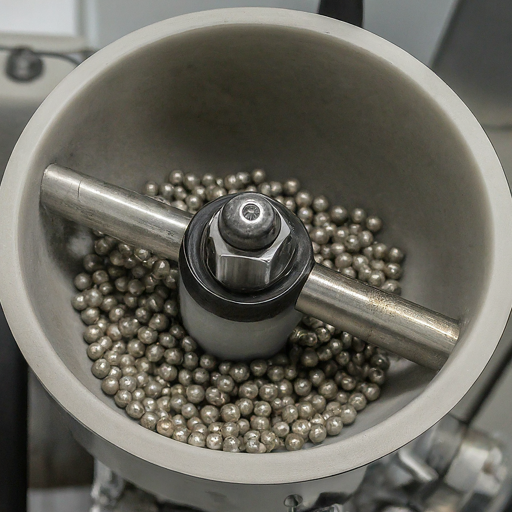
Principle: Utilize impact and attrition forces exerted by grinding media (balls) within a rotating chamber.
Applications: Suitable for grinding a wide range of ceramic glaze materials, including oxides, carbonates, and pigments.
Advantages: Versatile, capable of achieving fine particle sizes, and suitable for both wet and dry grinding.
Attritors
Principle: Employ high-speed impellers to create a turbulent media-powder mixture, resulting in particle size reduction.
Applications: Effective for grinding hard-to-grind ceramic glaze components and achieving fine particle sizes.
Advantages: High efficiency, rapid grinding, and suitable for large-scale production.
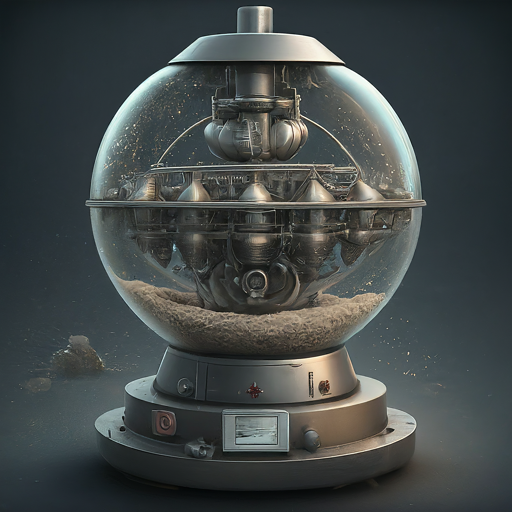
Jet Mills
Principle: Utilize high-velocity gas or air jets to collide and pulverize particles.
Applications: Suitable for producing ultrafine particles of ceramic glaze materials, especially for applications requiring high color intensity and dispersion.
Advantages: High-energy grinding, minimal contamination, and suitable for heat-sensitive materials.
Hammer Mills
Principle: Utilize rotating hammers to strike and crush materials.
Applications: Suitable for coarse grinding of ceramic glaze components, often used as a primary reduction step.
Advantages: High capacity, robust construction, and suitable for handling large feed sizes.
Factors to Consider When Selecting a Grinding Machine
Particle Size Requirements: Determine the desired particle size distribution for the ceramic glaze slurry.
Material Properties: Consider the characteristics of the glaze components, including hardness, abrasiveness, and moisture content.
Production Scale: Assess the required throughput and batch size.
Contamination Control: Evaluate the need for inert atmospheres or other measures to prevent contamination.
Energy Efficiency: Consider the machine's power consumption and overall efficiency.
Safety Considerations: Ensure the grinding machine has appropriate safety features.
Maintenance Requirements: Evaluate the ease of cleaning, component replacement, and overall upkeep.
Grinding Parameters for Ceramic Glaze Slurry
Grinding Media: Select suitable grinding media based on material properties and desired particle size.
Mill Speed: Optimize the rotational speed of the grinding chamber.
Grinding Time: Determine the required grinding duration.
Material Loading: Maintain the correct ratio of ceramic glaze slurry to grinding media.
Atmosphere Control: Consider using a controlled atmosphere (e.g., inert gas) to prevent oxidation or contamination.
Conclusion
Selecting the right grinding machine for ceramic glaze slurry is crucial for achieving optimal glaze properties and product quality. By carefully considering the factors outlined in this article, manufacturers can ensure efficient and effective grinding operations.
Keywords: grinding machine for grinding ceramic glaze slurry, ceramic glaze slurry, grinding equipment, ball mill, attritor, jet mill, hammer mill, ceramic, glaze, particle size reduction, manufacturing
Would you like to delve deeper into specific types of grinding machines or explore the challenges associated with grinding different ceramic glaze materials?