Introduction Zirconia ball mills, renowned for their exceptional hardness and wear resistance, are indispensable tools in various industries. However, their optimal performance and longevity depend heavily on proper maintenance and care. This article delves into the critical aspects of zirconia ball mill maintenance, employing a mechanical design perspective to provide a comprehensive understanding of the underlying principles and practices.
Understanding Zirconia Ball Mills
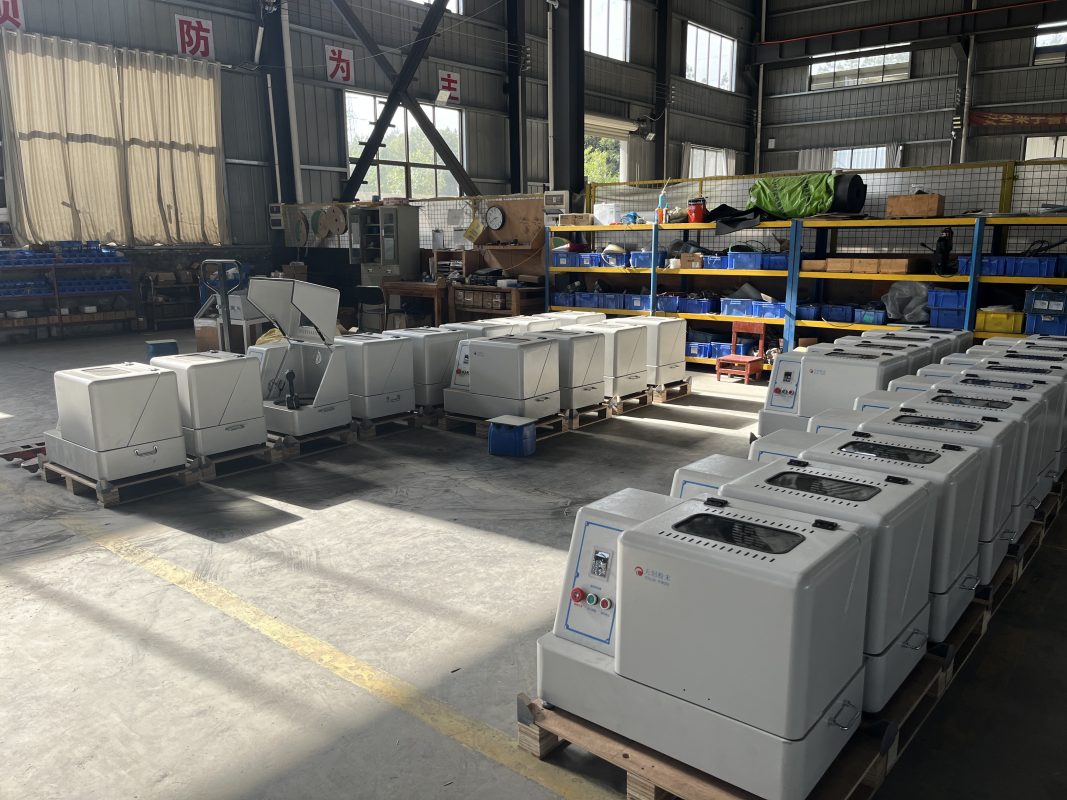
Before delving into maintenance, it’s essential to grasp the fundamental components and operating principles of zirconia ball mills.
Components of a Zirconia Ball Mill
A typical zirconia ball mill consists of:
Mill shell: The cylindrical enclosure housing the grinding media and material.
Liners: Internal wear-resistant components that protect the mill shell and enhance grinding efficiency.
Grinding media: Zirconia balls of varying sizes that impact and grind the material.
Drive system: The motor and gear arrangement that rotates the mill.
Feed and discharge systems: Mechanisms for introducing and removing material.
Bearing and seal assemblies: Critical components for supporting the rotating mill and preventing material leakage.
Veiklos principai
Šlifavimo procesą sudaro šie etapai:
Material introduction: Feed material is introduced into the mill shell.
Grinding: The rotating mill causes the grinding media to cascade and impact the material, reducing particle size.
Material discharge: The finely ground product is discharged from the mill.
Factors Affecting Zirconia Ball Mill Life
The lifespan of a zirconia ball mill is influenced by several factors:
Material properties: Hardness, abrasiveness, and moisture content of the processed material.
Grinding conditions: Mill speed, feed rate, and solid-to-liquid ratio.
Grinding media selection: Size, shape, and quantity of zirconia balls.
Liners: Material, design, and condition.
Lubrication: Quality and frequency of lubrication for bearings and gears.
Operating environment: Temperature, humidity, and dust levels.
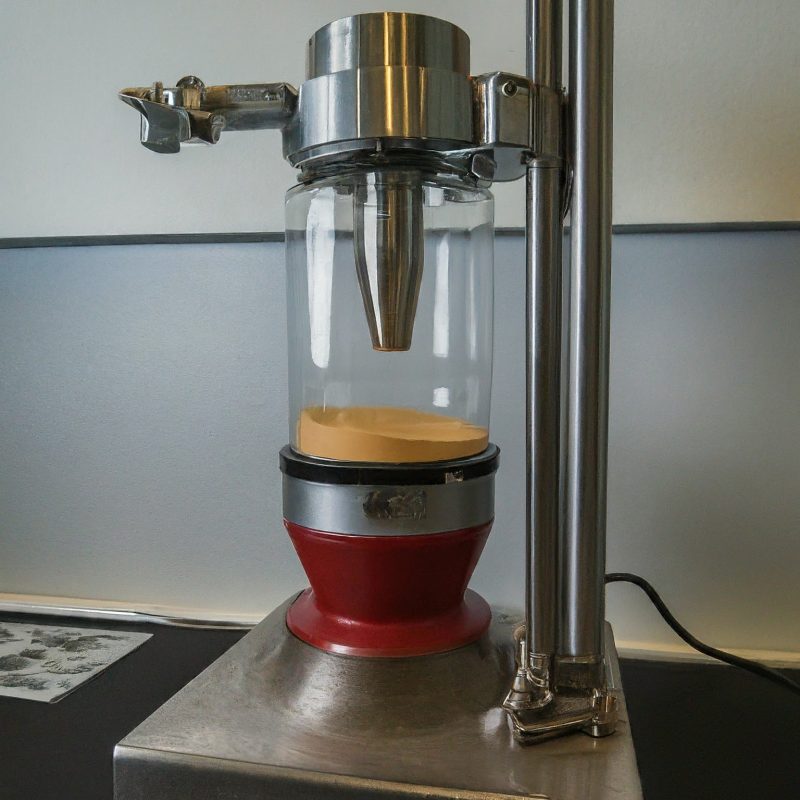
Maintenance Schedule
A well-structured maintenance program is crucial for maximizing the lifespan and efficiency of a zirconia ball mill. The following schedule outlines essential maintenance tasks:
Daily Inspections
Visual inspection for any signs of leakage, overheating, abnormal noise, or vibration.
Check lubrication levels in bearings and gears.
Monitor motor current and temperature.
Weekly Inspections
Thorough inspection of the mill shell, liners, and grinding media for wear.
Check for any damage to the drive system, including gears, couplings, and belts.
Clean the mill exterior and remove any accumulated material.
Monthly Inspections
Detailed inspection of bearings, seals, and couplings for wear or damage.
Check the alignment of the drive system.
Lubricate all moving parts as per manufacturer's recommendations.
Quarterly Inspections
Dismantle and inspect the mill for internal wear and damage.
Replace worn-out liners and grinding media.
Balance the grinding media load.
Clean the mill thoroughly, including the interior.
Annual Overhaul
Complete disassembly and inspection of all components.
Replace worn-out parts, including bearings, seals, and motor components.
Reassemble the mill and conduct a test run.
Preventive Maintenance
In addition to the scheduled maintenance, preventive measures can significantly enhance ball mill reliability:
Regular cleaning: Remove accumulated material and debris to prevent clogging and wear.
Proper lubrication: Use high-quality lubricants and adhere to recommended intervals.
Vibration monitoring: Detect early signs of imbalance or bearing issues.
Temperature control: Maintain optimal operating temperatures to prevent overheating.
Operator training: Ensure operators are well-versed in safe operating procedures and maintenance tasks.
Bendrų problemų šalinimas
Understanding common problems and their solutions is essential for efficient maintenance:
Excessive vibration: Check for imbalance, misalignment, worn bearings, or foundation issues.
Overheating: Inspect motor and bearings for proper cooling, check lubrication, and verify load conditions.
Material contamination: Implement strict cleaning procedures and prevent foreign material entry.
Reduced grinding efficiency: Evaluate grinding media wear, liner condition, and feed rate.
Bearing failure: Monitor bearing temperature, check lubrication, and replace worn bearings promptly.
Safety Considerations
Safety is paramount during zirconia ball mill maintenance. Adhere to the following guidelines:
Lockout/tagout procedures: Isolate power sources before working on the mill.
Personal protective equipment (PPE): Wear appropriate safety gear, including gloves, safety glasses, and hearing protection.
Confined space entry: Follow proper procedures when working in enclosed spaces.
Material handling: Use proper lifting equipment and techniques.
Emergency procedures: Develop and implement emergency response plans.
Conclusion
Proper maintenance and care of a zirconia ball mill are vital for ensuring optimal performance, product quality, and equipment longevity. By following the guidelines outlined in this article, you can significantly extend the life of your zirconia ball mill while minimizing downtime and operational costs.