Within the realm of scientific inquiry,
meticulous sample preparation is the foundation upon which countless discoveries are built. A crucial instrument in this preparatory process is the lab grinder, a workhorse dedicated to the size reduction of solid materials. This article, drawing inspiration from the comprehensive approach of Machinery’s Handbook, delves into the world of lab grinders, exploring their principles, functionalities, and applications.
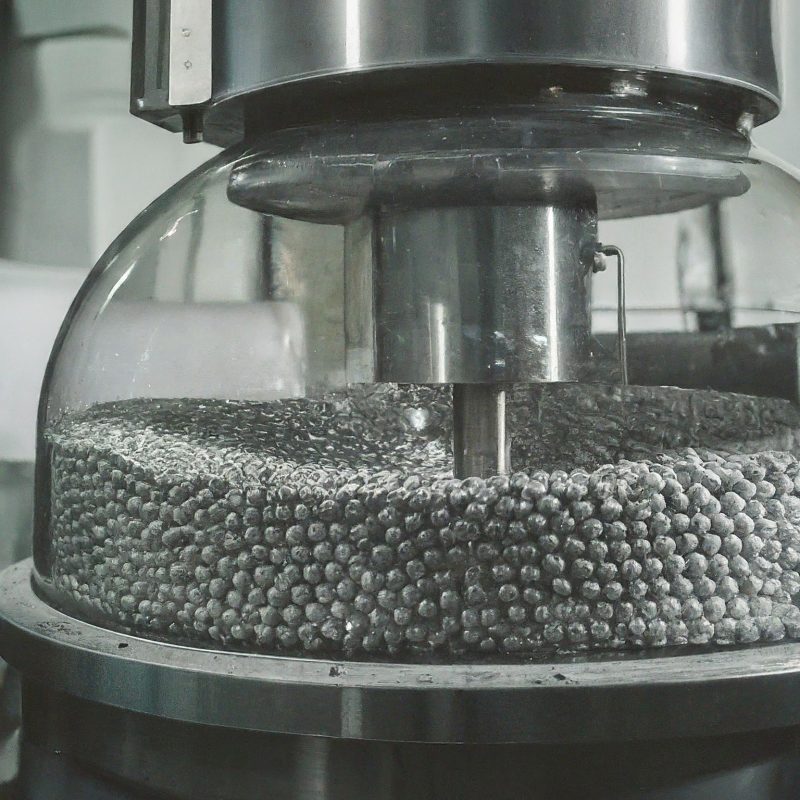
- Introduction
Across diverse scientific disciplines, the need to analyze the properties of solid materials arises frequently. Whether studying the composition of minerals, analyzing pharmaceutical formulations, or characterizing polymers, obtaining a representative sample in a finely divided form is paramount. Here’s where the lab grinder steps in.
These compact yet powerful machines utilize various size reduction mechanisms to transform coarse materials into fine powders. By precisely controlling the grinding process, scientists can achieve the desired particle size distribution, enabling a multitude of analytical techniques.
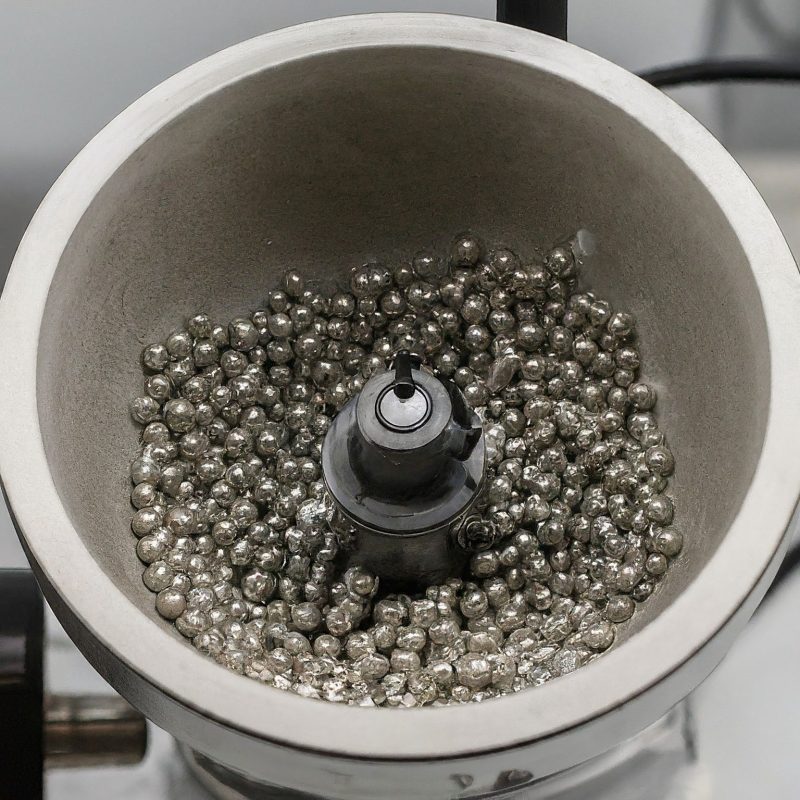
- Classification of Lab Grinders
The diverse landscape of lab grinders encompasses a range of technologies, each with its own strengths and limitations. Here’s a breakdown of some prominent types:
Hammer Mills: These workhorses employ high-speed rotating hammers that pulverize the material upon impact. They excel at processing brittle materials like grains, seeds, and pharmaceuticals.
Disc Mills: Utilizing one or two rotating discs, these grinders offer a shearing and grinding action. They are suitable for grinding a wide range of materials, including soft and fibrous materials, with minimal heat generation.
Cutting Mills: Featuring sharp blades that rotate at high speeds, cutting mills excel at grinding elastic or fibrous materials like plastics, rubbers, and food products.
Ball Mills: These miniature versions of their industrial counterparts utilize a rotating cylindrical chamber filled with grinding media (typically balls) to achieve size reduction through impact and attrition. They are well-suited for grinding hard and brittle materials to a very fine powder.
Mortar and Pestle: While not strictly a machine, the classic mortar and pestle remains a valuable tool for small-scale grinding applications, particularly in educational settings or for the preparation of very small samples.
- Operating Principles
Despite the varying mechanisms employed by different lab grinder types, certain core principles govern their operation:
Feed Material: The material to be ground is introduced into the mill's feeding hopper. The feed rate, which can be manual or controlled automatically, significantly impacts the grinding process and final particle size.
Grinding Mechanism: Depending on the mill type, the material is subjected to various forces—impact from hammers, shearing between discs, cutting by blades, or impact and attrition from grinding media. These forces progressively reduce the particle size.
Particle Size Control: Several factors influence the final particle size, including the type of grinder, the grinding media (for ball mills), the rotational speed, and the grinding time. Lab grinders often incorporate adjustable settings to control these parameters, allowing for precise control over the product size distribution.
Discharge: The ground material exits the mill through a discharge port, typically collected in a container for further analysis.
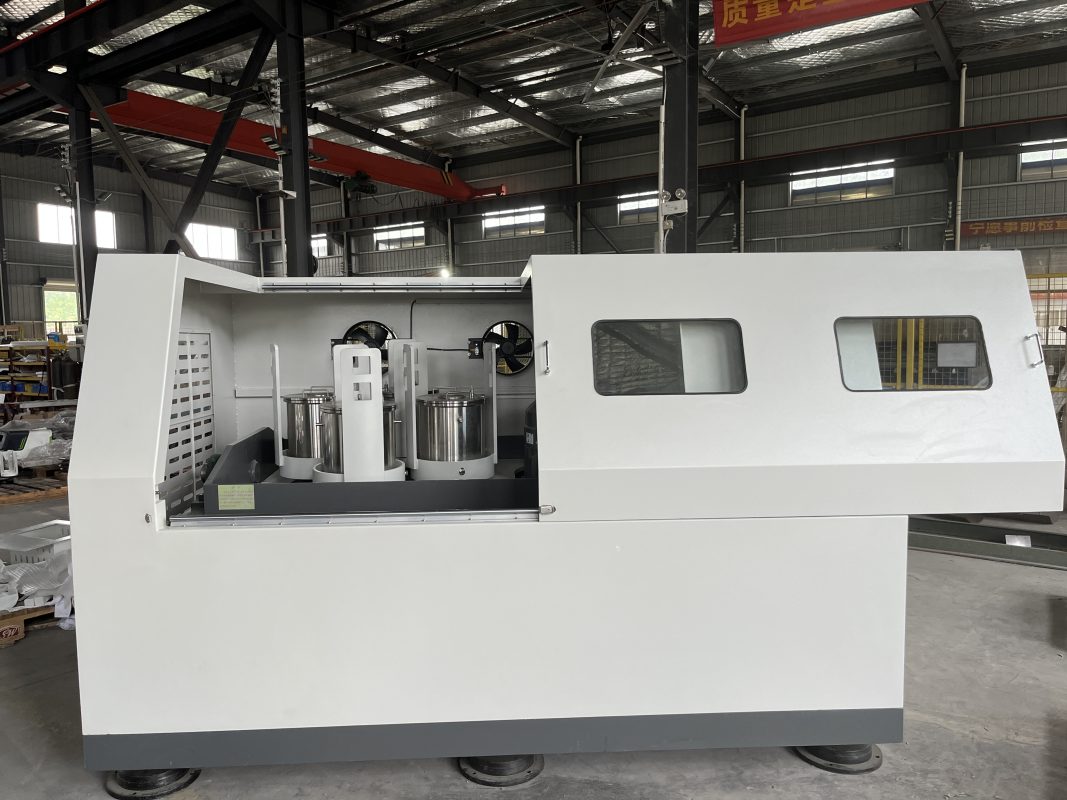
- Key Design Considerations
Effective lab grinder design prioritizes several crucial factors:
Versatility: Ideally, a lab grinder should be capable of processing a wide range of materials with varying hardness and friability. This might involve features like adjustable grinding mechanisms or interchangeable grinding chambers.
Particle Size Control: Precise control over the final particle size distribution is essential for many analytical techniques. The ability to adjust grinding parameters like rotational speed or grinding time is crucial.
Reproducibility: Lab grinders should deliver consistent results, ensuring the reproducibility of experiments. Reliable control systems and optimized grinding mechanisms contribute to this goal.
Ease of Operation: User-friendly interfaces, intuitive controls, and easy cleaning procedures enhance the overall user experience and streamline workflow efficiency.
Safety: Safety features like interlocks and dust collection systems are essential to prevent accidents and protect users from exposure to airborne particles.
- Applications of Lab Grinders
Lab grinders play a vital role in sample preparation across a multitude of scientific disciplines:
Chemical Analysis: Grinding is often necessary for analyzing the chemical composition of solid materials in techniques like X-ray diffraction (XRD) or elemental analysis.
Pharmaceutical Development: Formulation development and quality control of pharmaceuticals rely on finely ground samples for analysis of active ingredients and excipients.
Material Science: Characterization of material properties often requires finely ground samples for techniques like scanning electron microscopy (SEM) or particle size analysis.
Food Science: Analyzing the chemical composition and physical properties of food products often necessitates grinding prior to analysis.
Environmental Science: Studying the composition of soil, sediments