- Introduction
In the meticulous world of scientific research, the manipulation of particle size plays a pivotal role in diverse disciplines. Laboratory grinding mills emerge as essential tools for this endeavor, enabling researchers to transform coarse materials into finely divided powders with a controlled size distribution. This article, drawing inspiration from the comprehensive approach of the American Mechanical Energy Handbook, delves into the classification of laboratory grinding mills, exploring their operating principles, performance characteristics, and factors influencing their effectiveness.
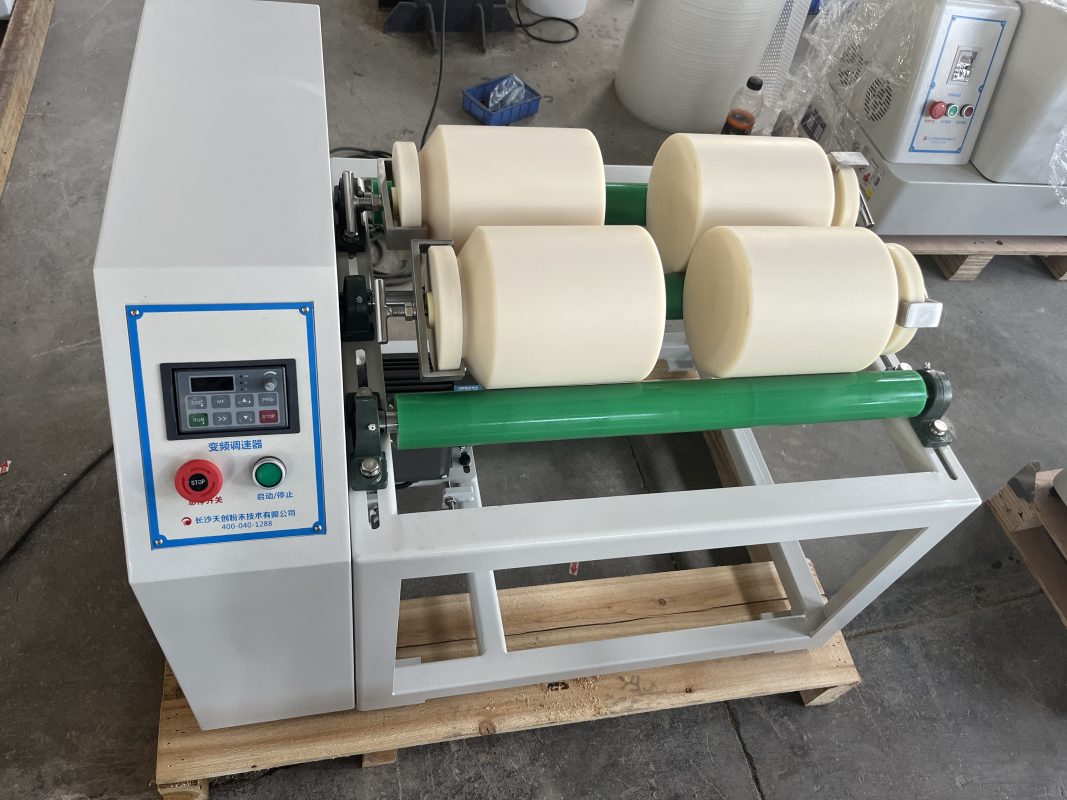
- The Grinding Mill Landscape: A Taxonomic Approach
The realm of laboratory grinding mills encompasses a diverse range of equipment, each with its own strengths and limitations. Understanding the various classifications is crucial for selecting the most appropriate tool for a specific research application.
Classification by Grinding Mechanism:
Ball Mills: These ubiquitous mills utilize a cylindrical chamber filled with grinding media (typically balls) that collide with the material to achieve size reduction. Ball mills further categorize into:
Tumbler Ball Mills: The chamber rotates on a horizontal axis, causing the grinding media to tumble and impact the material.
Planetary Ball Mills: The chamber rotates on a horizontal axis while simultaneously being carried by a larger, counter-rotating disc (sun wheel). This creates a complex, three-dimensional movement, enhancing grinding efficiency.
Mortar and Pestle Mills: This traditional method employs a manually operated pestle to grind material within a mortar. While simple and versatile, its application in research is often limited due to scalability and consistency issues.
Disc Mills: These mills utilize a high-speed rotating disc to shear and impact the material, achieving rapid size reduction. They are particularly suited for grinding brittle materials.
Cutting Mills: These mills employ rotating blades or knives to cut and fragment the material. They are suitable for processing fibrous or elastic materials that might not respond well to impact grinding.
Fluidized Bed Jet Mills: These mills utilize a high-velocity gas stream to propel grinding media particles against the material, achieving very fine particle sizes. They are often used for grinding heat-sensitive materials.
Classification by Grinding Mode:
Batch Grinding: Material is loaded into the mill chamber, and the grinding process occurs for a predetermined time. This mode offers flexibility but requires careful monitoring and control of grinding time for consistent results.
Continuous Grinding: Material is continuously fed into the mill, and the product is continuously discharged. This mode is ideal for high-throughput applications but necessitates careful design of feed and discharge systems to maintain consistent product quality.
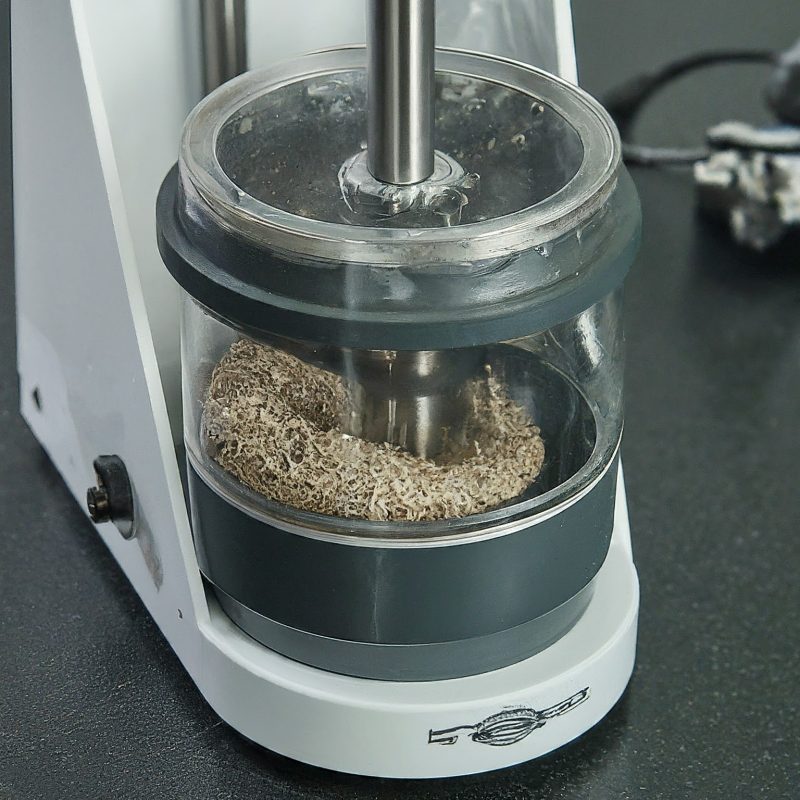
- Performance Evaluation: Key Metrics for Laboratory Grinding Mills
The effectiveness of a laboratory grinding mill can be evaluated based on several key performance metrics:
Particle Size Reduction: The primary function of a grinding mill is to reduce particle size. The ability of a mill to achieve the desired final particle size distribution is crucial. Performance is often evaluated using metrics such as median particle size (d50) and specific surface area (SSA).
Grinding Efficiency: This refers to the amount of energy required to achieve a specific particle size reduction. An efficient mill minimizes energy consumption while achieving the desired level of size reduction.
Contamination: Grinding media and mill components can potentially contaminate the processed material. Material compatibility and ease of cleaning are essential factors to consider.
Operational Simplicity: Ease of operation, including factors like loading/unloading, cleaning, and parameter adjustments, significantly impacts workflow efficiency.
Scalability: The ability to scale up grinding processes from a laboratory setting to a pilot or production scale is an important consideration for some applications.
- Factors Influencing Performance
Several factors influence the performance of a laboratory grinding mill:
Grinding Mechanism: The chosen grinding mechanism – ball milling, disc milling, cutting milling, or fluidized bed jet milling – significantly impacts the achievable particle size, processing efficiency, and potential for contamination.
Grinding Media Selection: The type, size, and quantity of grinding media play a crucial role. Factors like material hardness, shape, and size distribution influence the grinding action and final particle size.
Material Properties: The physical and chemical properties of the material being ground significantly impact the grinding process. Factors like hardness, friability, and moisture content influence the required grinding intensity and potential challenges.
Operational Parameters: Parameters like rotational speed, grinding time, and feed rate significantly influence the achievable particle size and processing efficiency. Optimizing these parameters is crucial for achieving desired results.
Mill Design Features: Factors like chamber size and geometry, material of construction, and cooling systems all play a role in overall performance and operational characteristics.