Advancing the Frontier of Electronic Glass Powder Grinding: A Comprehensive Look at Traditional Ball Mills and Our Revolutionary Solution
In the intricate world of electronics manufacturing, the quality of materials used is paramount. Electronic glass powders, with their unique properties like high thermal stability, low electrical conductivity, and excellent optical transparency, play a pivotal role in various components ranging from semiconductor wafers to display screens. The process of refining these powders into ultra-fine grains is crucial, and ball milling has been a long-standing method for achieving this. However, traditional ball mills for grinding electronic glass powders come with their share of limitations. This article delves into the shortcomings of these conventional machines and then showcases the groundbreaking advantages of our innovative ball mill specifically designed for electronic glass powder grinding.
The Challenges of Traditional Ball Mills for Electronic Glass Powder
- Energy Inefficiency: Traditional ball mills rely on heavy, rotating drums filled with grinding media (balls or rods) to crush and grind the material. This process is inherently energy-intensive, especially when dealing with hard and abrasive materials like electronic glass. High energy consumption not only increases operational costs but also contributes to environmental concerns.
- Limited Grinding Efficiency: Achieving uniform and consistent particle sizes, especially in the nanometer range, is a significant challenge with traditional ball mills. The grinding process can be uneven, leading to a wide distribution of particle sizes, which can compromise the performance of electronic devices.
- Wear and Tear: The abrasive nature of electronic glass powder causes significant wear on the grinding media and the mill’s internal components. Frequent replacements of worn-out parts and media add to the operational expenses and downtime.
- Contamination Risk: During grinding, the possibility of contamination from the mill’s materials (e.g., steel balls, mill liners) can adversely affect the purity of the electronic glass powder, which is crucial for its intended applications.
- Noise and Vibration: The mechanical action of ball mills generates significant noise and vibration, which can create an uncomfortable working environment and potentially damage surrounding equipment.
Introducing Our Revolutionary Ball Mill for Electronic Glass Powder Grinding
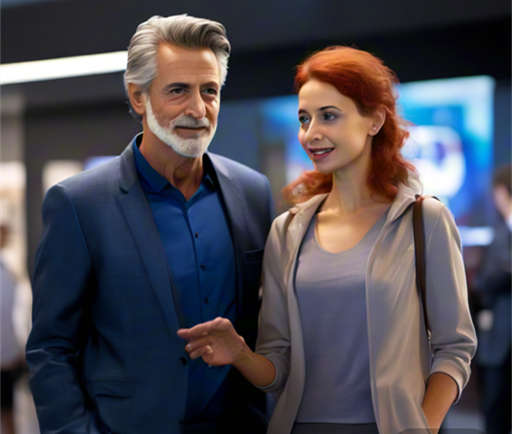
In response to these challenges, we have developed a cutting-edge ball mill specifically tailored for the grinding of electronic glass powders. Our solution addresses each of the aforementioned drawbacks, offering unprecedented performance and efficiency.
- Energy Efficiency and Sustainability: Our ball mill incorporates advanced energy-saving technologies, such as optimized motor efficiency and intelligent control systems, that significantly reduce energy consumption compared to traditional models. Additionally, we use high-quality, low-friction bearings and components to minimize energy loss during operation. This not only decreases operating costs but also aligns with the industry’s push towards more sustainable manufacturing practices.
- Precision Grinding for Ultra-Fine Particles: Our mill is equipped with advanced grinding dynamics and innovative media configurations that enable precise control over the grinding process. This results in a narrower particle size distribution, with a higher percentage of particles falling within the desired range. For electronic glass powders, this translates into superior material properties and improved performance in electronic devices.
- Durability and Reduced Wear: Recognizing the abrasive nature of electronic glass powder, we have designed our mill with specialized materials that exhibit exceptional wear resistance. The grinding media and mill liners are made from high-performance ceramics or special alloys that minimize wear and extend the machine’s lifespan. This not only reduces operational costs but also minimizes the risk of contamination from worn-out parts.
- Purity Preservation: To ensure the purity of the electronic glass powder, we have implemented rigorous contamination control measures. Our mill is constructed from non-reactive materials, and all contact surfaces are carefully selected to avoid any chemical interaction with the powder. Furthermore, we offer optional inert gas purging systems to create an even more controlled environment during grinding.
- Low Noise and Vibration: Our ball mill features advanced vibration dampening technologies and sound insulation measures, significantly reducing noise and vibration levels. This creates a more comfortable working environment and protects nearby equipment from potential damage.
- Automation and Intelligence: Integrating the latest automation and sensor technologies, our ball mill can be remotely monitored and controlled, providing real-time data on operating parameters and performance metrics. This enhances process control, optimizes grinding efficiency, and enables predictive maintenance, further reducing downtime and improving overall productivity.
Conclusion
In conclusion, the traditional ball mills for grinding electronic glass powders face numerous challenges, including energy inefficiency, limited grinding precision, excessive wear and tear, contamination risks, and noise pollution. Our revolutionary ball mill, on the other hand, addresses these limitations head-on, offering a comprehensive solution that prioritizes energy efficiency, precision grinding, durability, purity preservation, low noise, and intelligent automation. By choosing our ball mill, manufacturers can expect to produce higher-quality electronic glass powders, reduce operational costs, and contribute to a more sustainable future.